November 15th, 2018 | by Piotr Staniek
Additive Manufacturing Fuels Automotive Industry
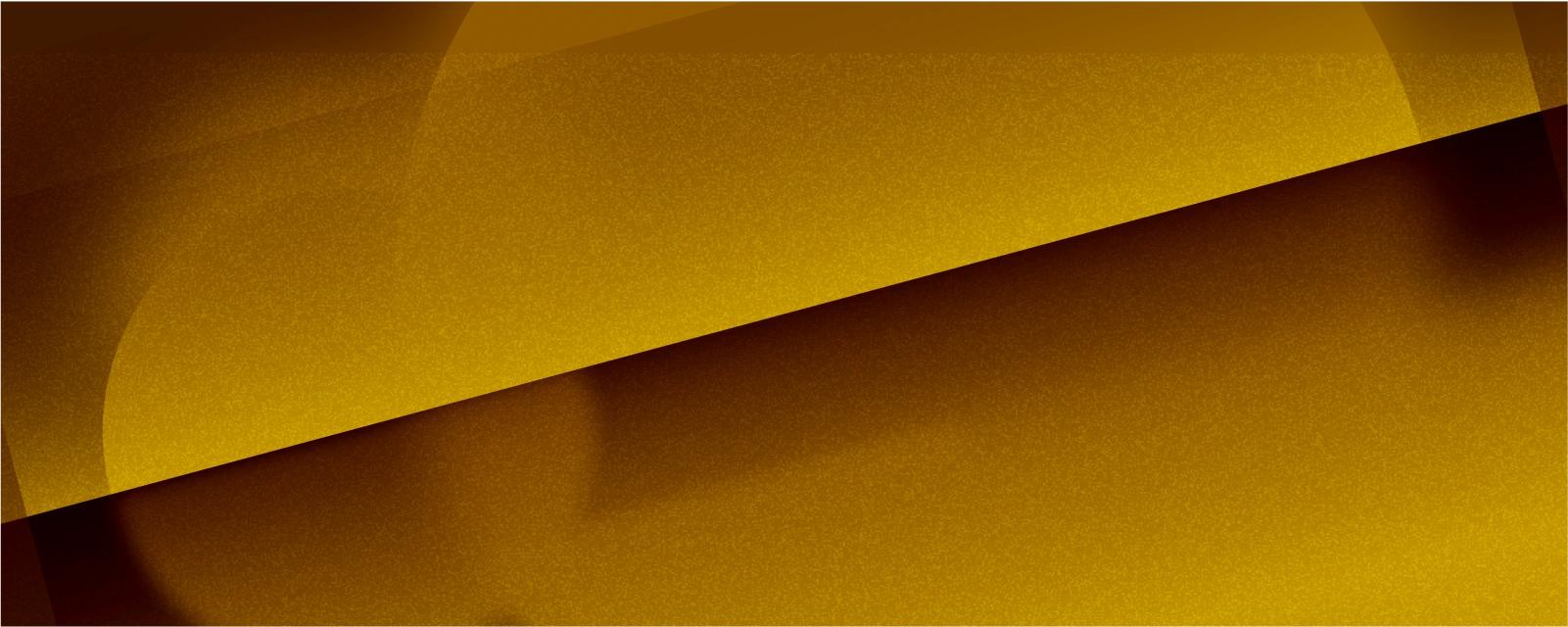
Table of contents
The Additive Manufacturing (AM) is often defined as the process of combining materials to create objects from a 3D model. It’s done layer by layer, as oppose to traditional and subtractive manufacturing processes. It’s futuristic, effective and budget-friendly. How does it work and how can you benefit?
Additive Manufacturing
Additive Manufacturing is full of benefits:
- Accelerated product development
- Manufacturing process simplification
- Design flexibility
- Mass customisation opportunities
- Cost optimization
What encourages automobile manufacturers to integrate 3D printing processes into their production strategy and daily product development are:
- Short lead times
- Access to new materials
- Access to new finishes
This is the data taken directly from Technavio’s report on Additive Manufacturing. Metal additive manufacturing is used for the production of various automobile parts. Among them are pumps, windbreakers, cooling vents and valves. Bumpers too, but these are too obvious in this company. Accelerated production in Automotive is possible with not only 3D printing itself but with the presence of innovation in such areas as tool design, machine programming, testing and optimization, certification, computer simulation and modelling. Let’s not forget that Additive Manufacturing is not a lone island, it has to draw from its natural environment in order to thrive. That way a transition from rapid prototyping into the production of complex parts can be made. From pre-production, visualisation, modelling and proof-of-concept to end-use products that drive revenue.
Read also: Digital Transformation for Automotive Manufacturers and Suppliers
Traditional manufacturing methods based on carving or shaping a product is being replaced by two significant pole shifts: a model in which 3D printing is the only one available and the one that combines new techniques with traditional bulk metal forming. This allows for the creation of hybrid manufacturing.
The Additive Manufacturing is known for one other, significant advantage. In the traditional manufacturing process, some costs can and often are hidden from management. This is due to the supply chain, which is responsible for blurring the real image of the spending structure. The AM has an enormous impact on the design and size of the not only the production process itself but also on the factory ecosystem. After all, complicated assembly lines will not throw away themselves.
According to the previously mentioned report by Technavio, experts tell us that value of Addictive Manufacturing will reach $50 billion between 2029 and 2031 with $100 billion between 2031 and 2044. That’s a huge potential and Automotive will be responsible for a lot of revenue.
3D printing in the automotive industry is not only manufacturing itself. The real deal is called ‘spare parts’. By shortening the supply chain and optimizing costs, companies will have the opportunity to offer customization options for literally every single customer that walks into the showroom. That goes for customization of the bumper, rear mirror and some other, more exquisite parts as well. Spare parts market will grow, fuelled by delivery capabilities, price drops and availability. Not to mention short time-to-market.
Not everything is so fine and dandy, though. Machine and raw materials is still a serious factor, holding back changes in many sectors. Not only Automotive but Aerospace as well. The usage costs of AM machines can be limited by volume factor – the more you produce, the cheaper it gets. Nesting parts in a special chamber, for example, allows for the production of many parts in a single batch. Unfortunately, it raises the issue of part traceability and certification – it’s just harder to do in this case.
Let’s forget experimental cars like Urbee, first released in 2011, with the 2nd version a few years later. AM for Automotive goes beyond 3D-printed frames.
Read also: Automotive Retrofitting – An Old Car Is New Again
In 2013 alone, there were 86 million cars produced, globally (1). Even if the adoption rate will reach let’s say 25%, it will be challenging for the industry to manufacture large parts. Build envelopes are limited and even with constantly pushing innovations (see our blog post on EuroBLECH 2018) we have to give specialists some time.
Another problem is a little less obvious one. AM products can’t be copyrighted but can and even have to be patented. The lack of clarity on the matter of patent protection, there is a real chance of the proliferation of counterfeit components. According to the market research company Gartner, the global market of parts in end consumer-related industries (toys, IT) could be worth as much as $15 billion in intellectual property theft. And that’s for 2016 alone. (2)
Read also: Industry 4.0 Sector – Responsiveness that Leads to Improvement
On a happy note – there are savings everywhere you look. Volkswagen Autoeuropa is able to save thousands of Euros because of the company 3D prints tools for workers on assembly lines. 3D printing means new materials, which translates into the possibility for some crazy stunts. McLaren, for example, produced a new race car wing in just under two weeks. Using a 3D printed ULTEM1010 mold tool for the creation of the shape of the wing, they improved the manufacturing process. Similarly, Team Penske’s team of IndyCar and NASCAR was able to use Additive Manufacturing for printing master patterns and direct molds. The team reduced production time by 70% (!) since then.
An interesting case study can be shown through the experiences of a Husarion. This company has built its own 3D printer for rapid robot mechanics prototyping. They also use it for the production of some mechanic elements of their robots. As says Dominik Nowak, Husarion’s CEO:
A 3D printer is invaluable for prototyping, it significantly reduces time-to-market. We deeply care about aesthetics, quality and functionality. When that’s assured, we can go for injection mold and mass production. In some cases – especially in small volumes – manufacturing the mold is not economically justified; 3D print is a solution is assuring the sane unit cost.
First we bought some 3D printers from an open market. It quickly turned out, that a small working field and the lack of heated table were a major inconveniences. We turned into building a printer of our own; our employees worked on them as a side project. It was a great idea – now we can quickly show our customers how easy it is to build robots based on our technology.
On a more technical note – it’s not that hard to build a printer if you have a necessary expertise and have great developers. There are some open source projects like Marlin. Making a firmware to 3D printer is limited to modifying of a configuration file and porting the software for your printer’s driver. There is also a large number of open source projects for communication with 3D printer from computer’s side, Slic3r is one of them. The biggest issue is with the hardware itself – you have to take care of engines, minimize empty space, assure the stable construction and heated table. Electronics are also crucial – engine controls, power and cooling systems can make or break the project. I would say that mechanics and electronics makes the 90% of the challenge here.
3D printing is not enough, though. If you’re shooting for a smart factory, you also need software product development. The brain behind the muscle, so to speak. The automation software plays a large role in automotive and its processes, powering up not only machines but also the delivery process. It is blood inside the vein, optimizing production. It also gathers and analyses data, therefore it helps managers to deliver and make decisions about pre-emptive maintenance efforts. What assembly or a part needs attention, resources, money, workers to replace or repair? In what time and when? The answers to these questions can save thousands or even millions of dollars annually. Look for the right vendor for software development services and optimize your manufacturing process.
(1) IBISWorld, Industry report: Global car and automobile manufacturing, May 2013
(2) Pete Basiliere et al., “Predicts 2014: 3D Printing at the inflection point,” Gartner, 2013