October 8th, 2018 | by Radosław Szmit
How to Boost Production Efficiency Under Industry 4.0 by Using Automation Software?
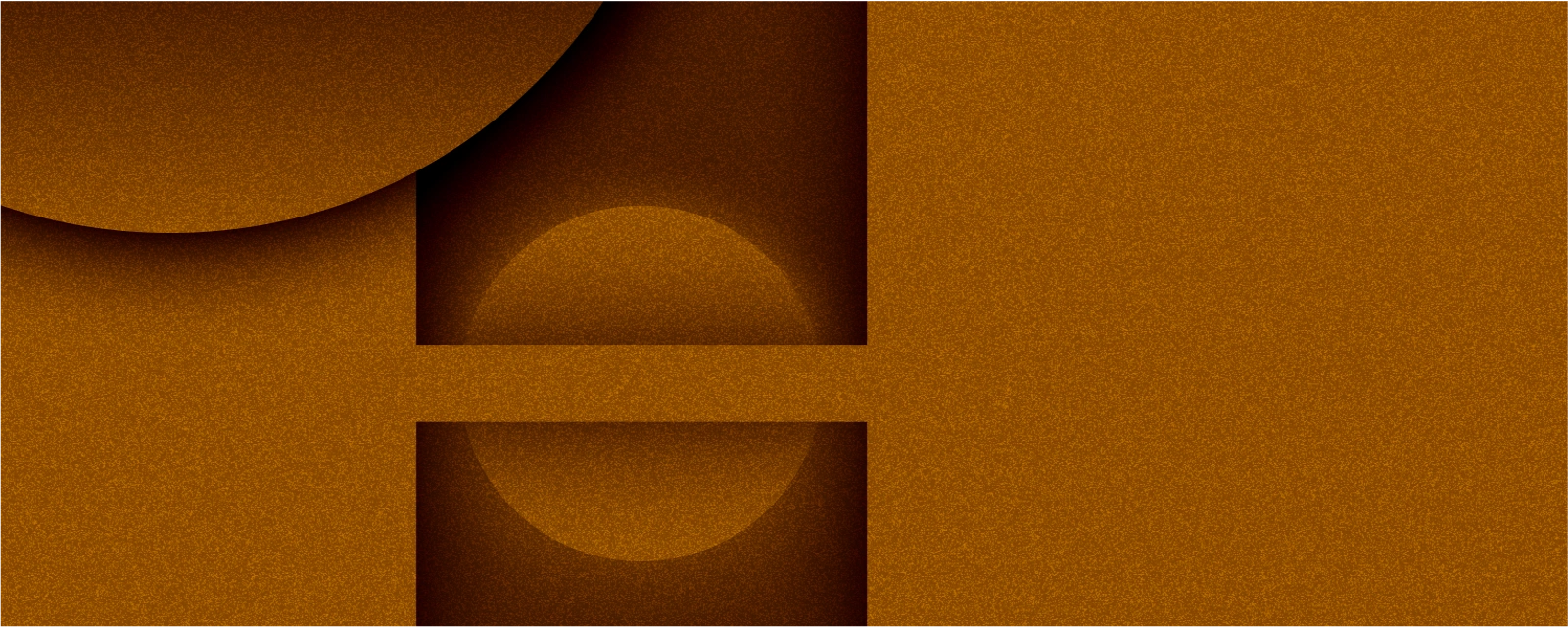
Table of contents
Under Industry 4.0, modern factory is no longer based on a linear system of assembly lines, with parts carried and implemented by workers. A 9 to 5 job model can be applied, but the old mentality definitely not. Thanks to automation software and product development services, efficiency can be significantly improved, giving the company much needed optimization of processes, expenditures, quality and revenue. How to make the change process painless and effective?
Automation software in smart factories
Please note that we didn’t use the phrase “if you want to make”. To be relevant, factories have to compete on a global scale. A price alone does not make the offer relevant. Complex offer consists of price, production efficiency, time and material needed to complete the order and the means to deliver. Automation software is a backbone of a modern, smart factory. Industry 4.0 requires ingenuity and efficiency; automation software largely contributes to the solution.
Chaos is the enemy of order. Message fragmentation across emails, excel files, phone conversations, messenger notes and many other potential agents of chaos can bring a company-wide catastrophe. That’s where a central database full of data about schedule, production order and working shifts comes in. Manager can oversee the production process and pull information about machine’s working condition, the level of wear and tear, employees on shift, product bandwidth on a line, etc.
Interesting implementation case of the automation software is with Hyundai Motor Company. The organization relied heavily on the outdated manual management system. Its use of Excel sheets to manage production status slowed down the entire rapid prototyping (RP) department. Keeping track of all produced parts was complicated and required additional manpower and man hours. It was also necessary to manually manage the operating plan for each machine. Adjustment and communication involving changes also were a thing. When Hyundai decided to introduce automation software, man hours were reduced by 77%. Company also saved material (13%), reduced data preparation time (astonishing 94%!), as well as build and post-processing time (significant 30%). Automation software and product development services enabled the company to not only produce prototypes faster but also to manage production with higher efficiency.
Introducing automation software into the automotive factory can also result in smooth sailing in another department – predictive maintenance. When repairs and maintenance are planned it can make companies double digits in cost savings. Automation software’s monitoring can help predict when forced maintenance may occur due to equipment breakdown and applies red flag to a particular tool. Due to a real-time condition monitoring the production can run as intended.
That’s not all, though. Factories are always under a tremendous pressure to deliver means for putting product on a shelf, so it’s imperative to fulfil the time-to-market request. According to last 2017’s PWC report on manufacturing industry, introducing mobile technology is crucial for 73% CEOs out there. Cyber security is next on a wish list for 72% managers and 70% executives speaks about the data mining and analysis as high priority. That’s not a coincidence, knowledge gives the upper hand on a market.
The challenge – you need software for that to work. The need for features like predictive maintenance, inventory management, invoicing or production time stamps are dictating the scope of company’s investments. How to choose the right software and software product development company that gets the job done?
Automation software for the factory under Industry 4.0
Automation software for the factory under Industry 4.0 has to:
- Allow for part tracking, its quality and traceability of the worker responsible for that part
- Give managers the option to review data at any given time to make necessary and real-time adjustments
- Give the customer the option to track the progress of an order. It’s a stage, completion percentage and total cost
- Inform the customer about possible bottlenecks along the way and implemented means to prevent them in the future
- Provide internal and external security when exchanging valuable data with cloud solutions, like e.g. IoT Husarnet platform
According to the Capgemini’s report on automotive smart factories in the digital industrial revolution, companies tend to go through three stages before they can optimize the manufacturing process (details on page 21):
- Struggling organizations develop a vision of the smart factory, identify its features and technologies under which it will run and secure funding for it
- Early-stage organizations adopt a management model, search for digital specialists to industrialize factory and its processes and adopt end-to-end digital transformation rather than point solutions
- Established or at least semi-established digitally-run organizations effectively incorporate smart factory solutions use KPIs to monitor progress and launch innovation initiatives
Before any factory can become smart factory its managers have to think about what automation really means. Automation software for the automotive industry is not a new concept. The true challenge is that software has to stay on top of any given tasks. That means it hast to be developed with possible updates and new features in mind. In that context, automation software is like automotive software intended to be implemented inside the car – it can’t end with start of production (SOP). Meaning the old model assumed (on paper and in reality), that the software product development ends with the start of car’s production cycle. The new model turns this philosophy upside down – now development starts with the actual start of car’s production.
The interesting example is Tesla, which embraced the model from the get-go. Tesla does over-the-air (OTA) updates, which sometimes creates chaos. Like with model Tesla S, that had shipped with cameras and sensors but without the software to run them, because it simply wasn’t complete.
According to previously cited Capgemini’s report, by 2022 automotive manufacturers expect that 24% of their plants will be smart factories and 49% of automakers have already invested more than $250 million in smart factories. It is time for the software to take over in factories and humans to oversee the production cycles. Automation software can be a deciding factor between big production order and new customer, and giant industry cutbacks. Are you ready to make a profit by investing in tools of tomorrow?