Arup
Empowering
Industry Leaders
From pioneering financial and regulatory solutions that redefine the industry’s landscape to groundbreaking transformations in next-gen manufacturing, and designing innovation, our portfolio is a testament to the transformative power of technology.
Dive Into Our Case Studies
Explore these real-world examples to discover how we overcome challenges, drive growth, and achieve remarkable results with our clients.
Financial & Regulatory
Our case studies in the FinTech & RegTech sectors showcase how we empower organizations to navigate the complexities of the financial landscape, ensuring compliance, efficiency, and unparalleled growth.
Industrial & Manufacturing
Our case studies in the industrial & manufacturing sectors spotlight how we empower organizations to overcome industry challenges, optimize operations, and achieve growth. Dive into these success narratives that set the standard for transformative advancements.
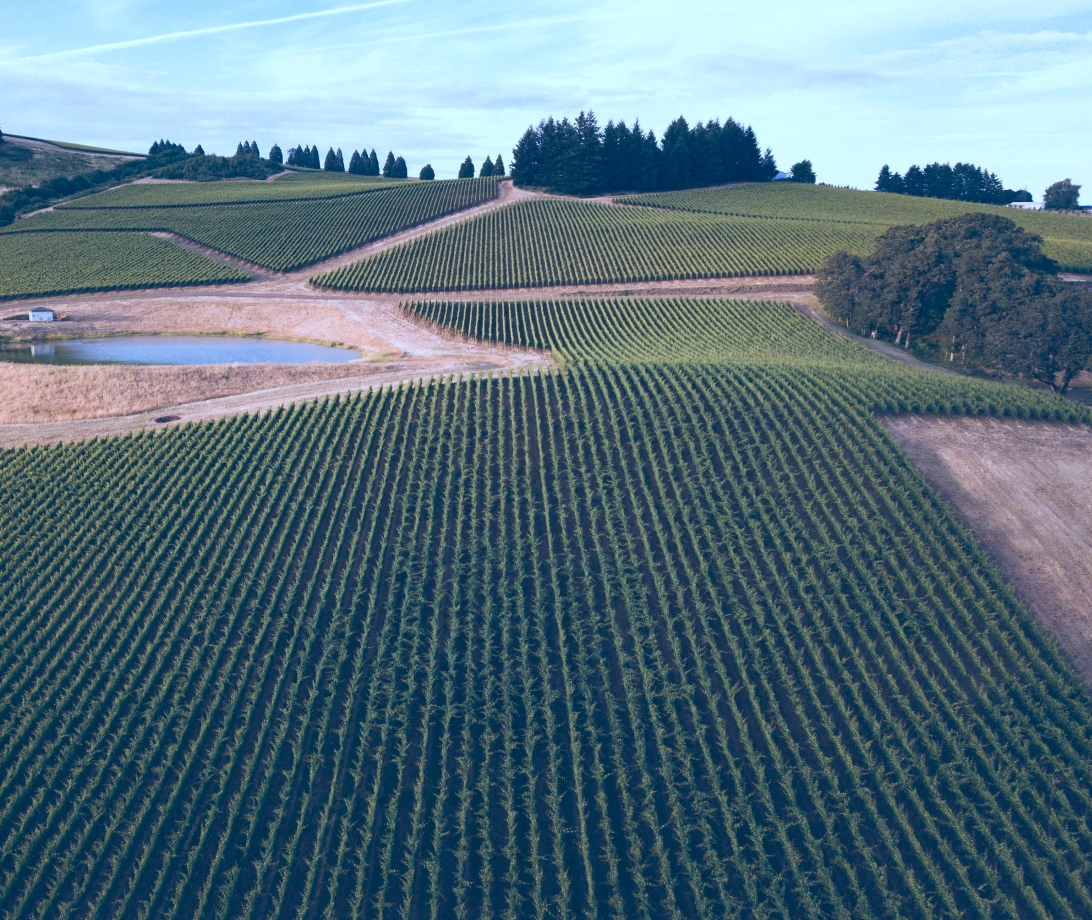
Designing Innovation
Delve into our case studies to uncover the art and science behind product design and explore solutions that redefine user experiences, making a lasting impact on brands in diverse industries.
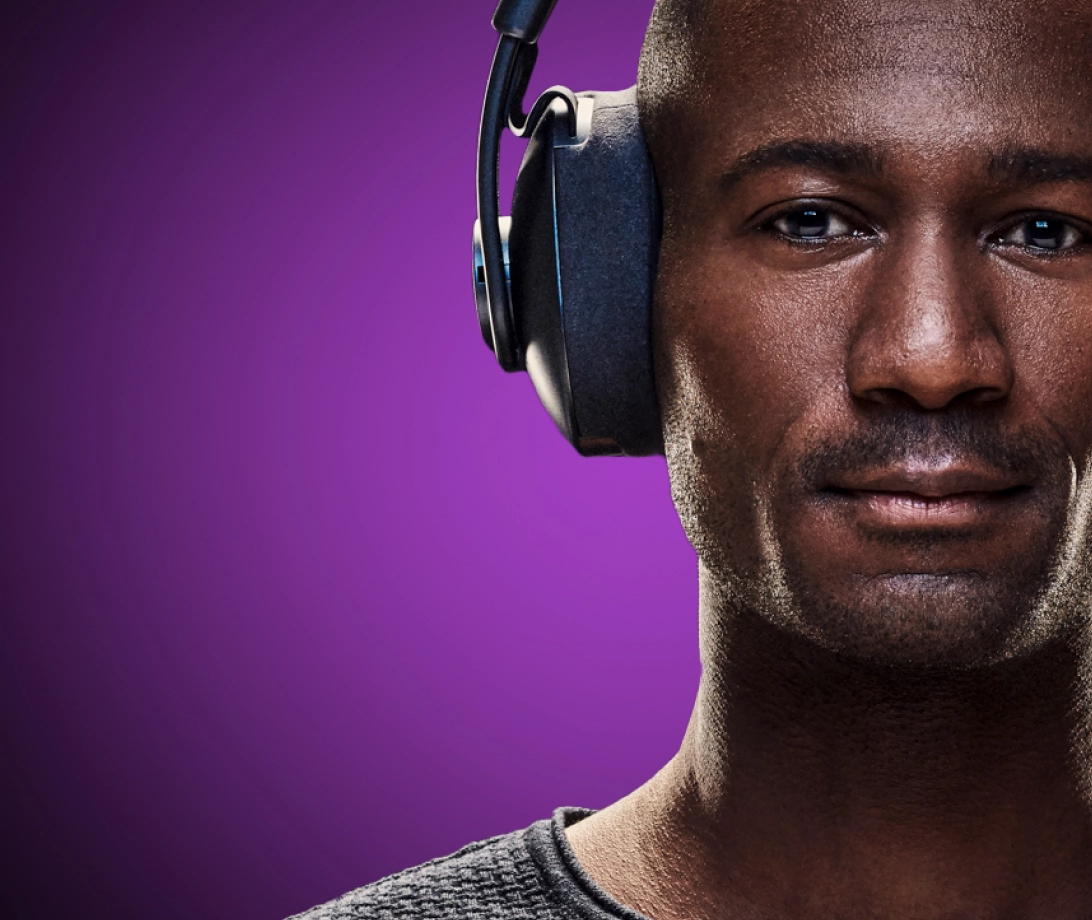
Eno
A Fresh Modern Take on Neurotechnological
E-Commerce Web Design
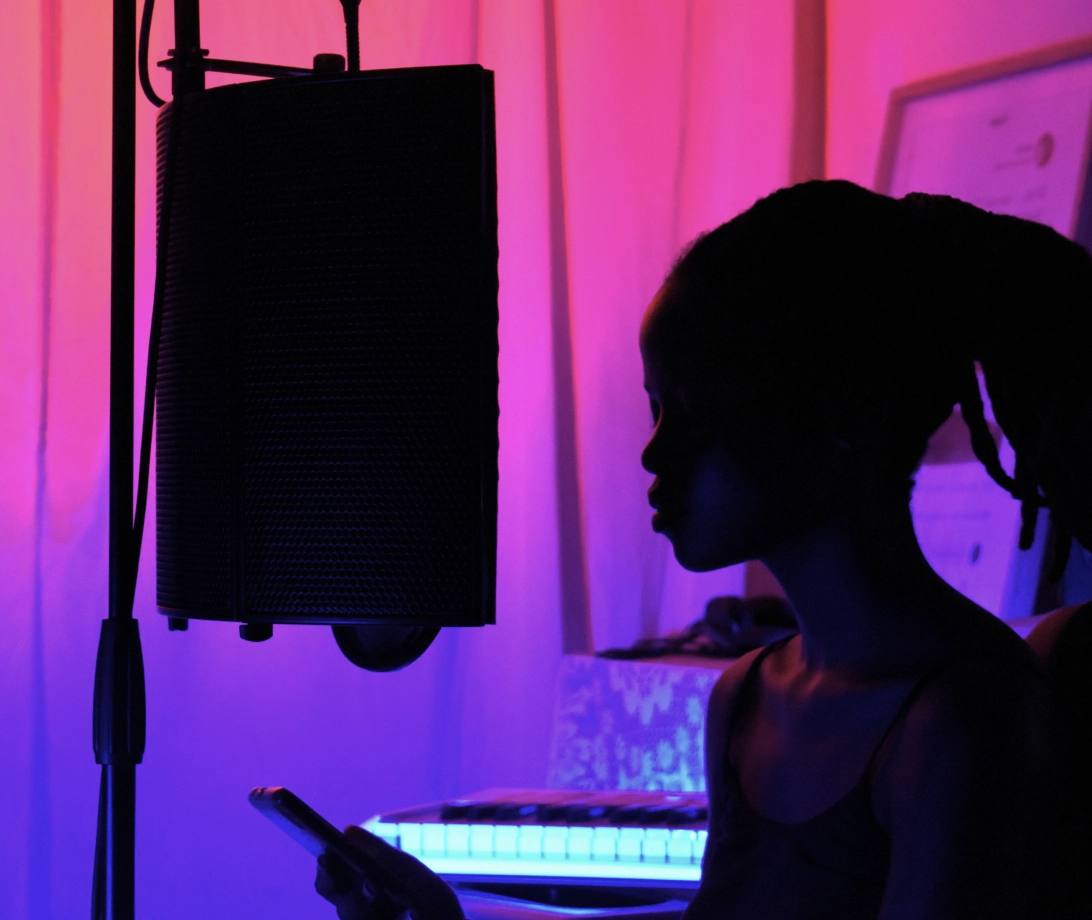
The Unsigned Library